ProtoShapes, Inc. offers prototype and production services for parts varying in size, weight, and quantity. Detailed design and tight specifications are no problem for our experts.
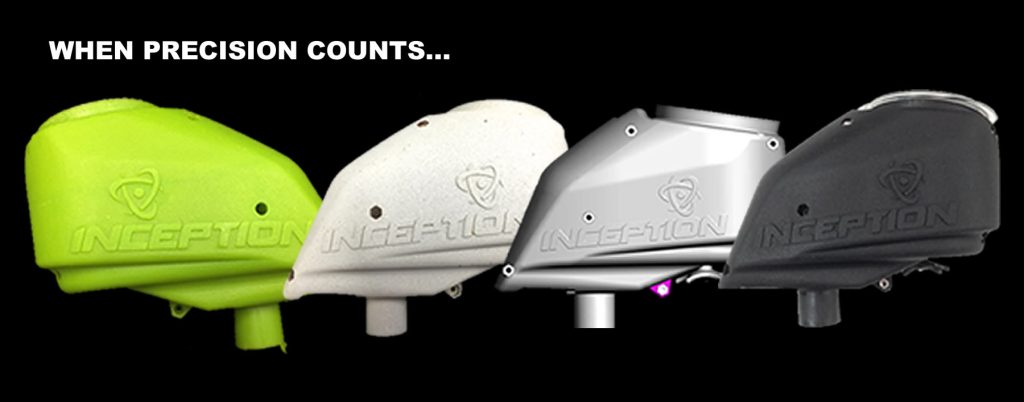
Storage and rerun services are available. Discuss your long-term parts production needs with our staff, we will have your parts ready when you need them!
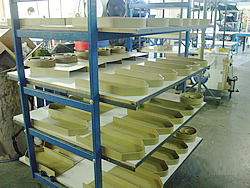
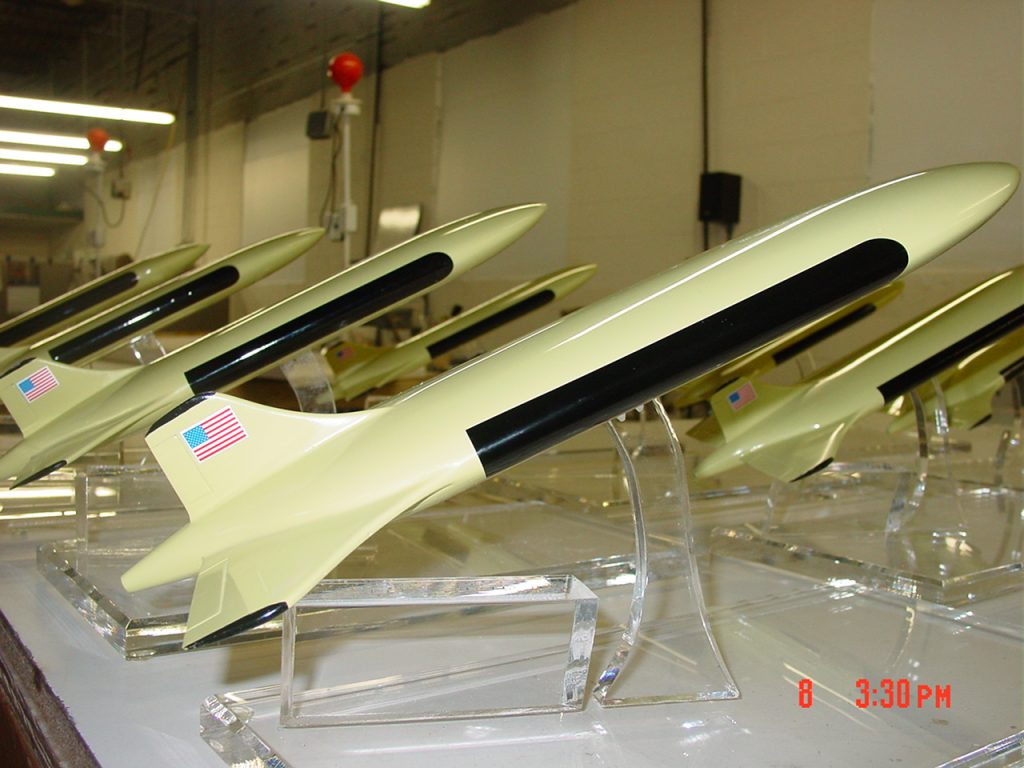
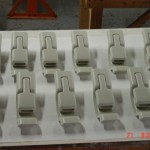
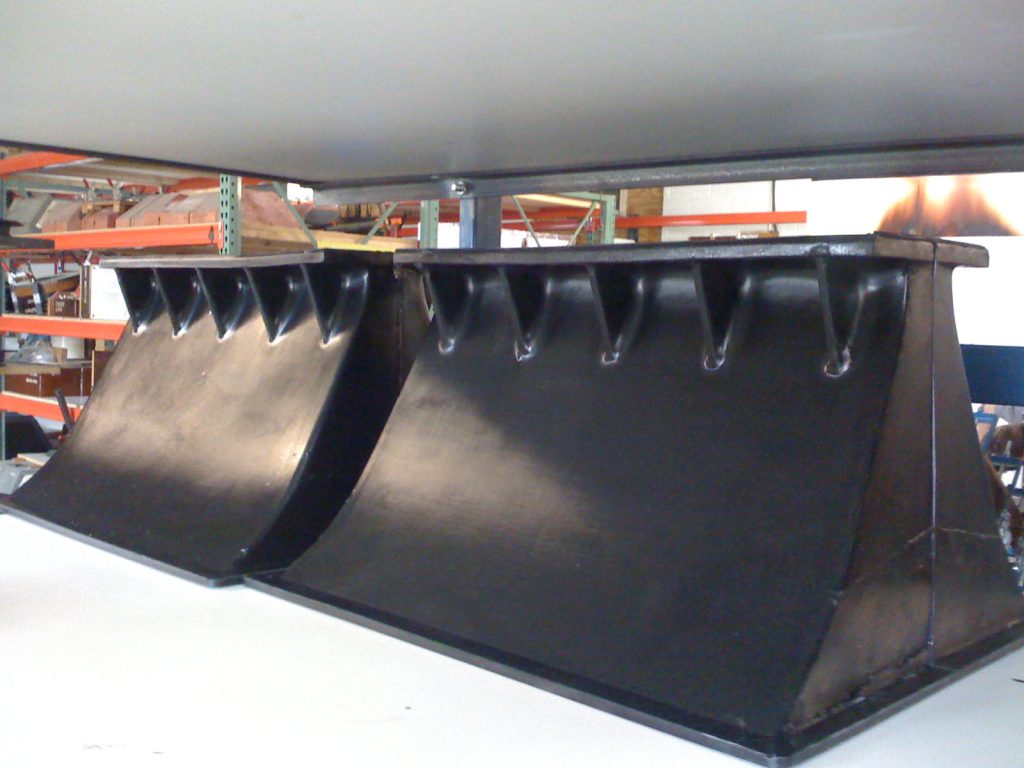
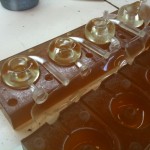
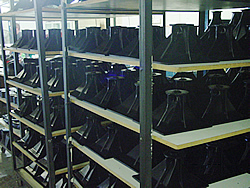
Polyurethane Materials
Polyurethane is an incredibly resilient, flexible, and durable manufactured material that can take the place of paint, cotton, rubber, metal and wood in thousands of applications across all fields. Polyurethane may be hard, like fiberglass, squishy like upholstery foam, protective like varnish, bouncy like rubber wheels or sticky like glue. Since its invention in the 40s, polyurethane has been used in everything from baby toys to airplane wings and continues to adapt to progressing techniques and technologies.
The chart and information below may help in assisting you with your material selection.
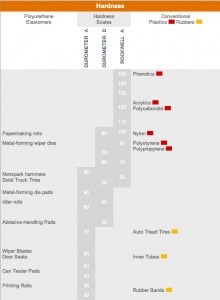
The hardness of a product is a good place to start in selecting a plastic or rubber for your parts. However, the hardness does not serve well as a predictor of other properties such as strength or resistance to scratches, abrasion, or wear, and should not be used alone for product design specifications.
To make the proper selection we can provide you with material spec sheets. You will find most of the information you need in this document. If a sample is required, please make that request.
Other Polyurethane Physical Properties To Consider:
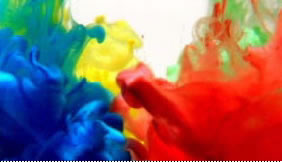
COLOR: In most cases a pigment can be added to the polyurethane system. Our favorite color is black, did we mention our favorite color is black!
ABRASION RESISTANCE: In applications where severe wear is a problem, polyurethane usually offers several times the wear life of ordinary rubber, plastic and even metal. In products such as solid tires, an eightfold improvement compared with conventional rubber is not uncommon.
FLAME RESISTANCE: Special formulated compounds of polyurethane, tested in accordance with ASTM D635 are self-extinguishing.
HEAT RESISTANCE: Products of polyurethane perform well at moderately elevated temperatures. The usual limit for continuous exposure is 165°F. Special formulated compounds of polyurethane can reach over 200°F.
IMPACT RESISTANCE: Polyurethane has significantly better impact resistance than structural plastic.
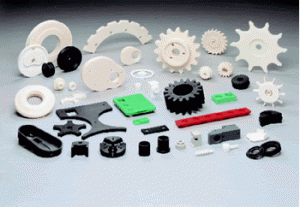
OIL AND CHEMICAL RESISTANCE: Polyurethane has excellent resistance to oil, solvents and many chemicals. Test results have shown polyurethane to last up to 20 times longer than rubber when immersed in truck oil and fuel.
ADHESION: During fabrication of composite parts, polyurethane can be readily adhered to many metals, elastomers and plastics, with bond strengths that often exceed the tear strength of the polyurethane itself.
COEFFICIENT OF FRICTION: Polyurethane has a low unlubricated coefficient of friction. This characteristic, coupled with its superior abrasion resistance and load-bearing capacity, is an important reason for its use in bushings and bearings.
FLEX PROPERTIES: Polyurethane resists cracking under repeated flexure, as evidenced by its successful use in many dynamic applications. Our polyurethane can be used in very thin sections because of its exceptional strength and toughness.
MACHINEABILITY: The machineability of polyurethane approaches that of some metals and is similar to many plastics. It can readily be drilled, routed, sawed, or turned and shaped on standard metalworking equipment by experienced operators familiar with normal procedures for handling plastics.
Rubber Parts with Your 3D Printer
There are different ways to obtain rubber parts utilizing your 3D printer. Some 3D printers, like Objet, can print rubber-like materials. However, the physical properties are poor. Another way is to 3D print a mold and then compress rubber (like Sugru) into the mold.
Better yet is to simply print out your part with your typical 3D printer plastic to make polyurethane cast parts. Send this part or pattern to us and we will build a tool to cast your rubber parts.
If your 3D Printed Rubber parts require improved functionality, detail and stability, read more to see what ProtoShapes, Inc. can do for you!
Major advantages of polyurethane cast parts:
- Rubber variety. Many different formulations of polyurethane can be casted into the tooling to achieve desired physical properties. Such properties include: hardness, rebound, flexural strength, chemical resistance, dielectric and abrasion resistance, to name a few.
- Time. It only takes us a few days to render tooling for your pattern. Most of our polyurethane rubber is catalyzed to form parts in minutes. With the use of precision meter mixing equipment we can ensure consistency and quality parts.
- Quantity. We can produce a few parts to thousands on demand, if required. Depending on the requirements of the run, multiple tools can be built to increase the needed output.
- Quality. Upon receipt of your pattern, we will cleanup and add a fine texture to cosmetically give the part an OEM look.
- Cost. Polyurethane cast parts cost much less than other processes, unless you go to high volume steel tooling. The trade-off may be the tooling cost. But if you are looking at low volume production or just a few prototypes, there is no doubt polyurethane castings will prove more cost effective.